数控雕刻机加工中,应首先确定雕刻材料的加工原点(工件原点),以建立准确的加工坐标系,同时考虑刀具的不同尺寸对加工的影响。对刀的精度决定零件的加工精度,同时,对刀效率还直接影响雕刻加工效率,这些都需要通过对刀来解决。
1、一般对刀
一般对刀是指在数控木工雕刻机上使用相对位置检测手动对刀。下面以Z向对刀为例说明对刀方法,刀具安装后,先移动刀具手动雕刻工件右端面,再沿X向退刀,将右端面与加工原点距离N输入数控系统,即完成这把刀具Z向对刀过程。手动对刀是基本对刀方法,但它还是没跳出1325木工雕刻机的“试切--测量--调整”的对刀模式,占用较多的在机床上时间。此方法较为落后。
2、机外对刀仪对刀
对刀仪对于浮雕机雕刻的客户很重要重要。对刀仪极大的方便用户确定Z轴的工作零点位置,在雕刻加工过程中如出现断刀、粗精加工更换不同型号的刀具等都可以利用对刀仪来完成精确地Z轴定位。用户必需将对刀仪块的厚度输入到参数中,执行文件时系统自动将零点位置下移对刀仪块厚度的深度,这样才能真正确定了Z轴工作零点。机外对刀的本质是测量出刀具假想刀尖点到刀具台基准之间X及Z方向的距离。利用机外对刀仪可将刀具预先在机床外校对好,以便装上机床后将对刀长度输入相应刀具补偿号即可以使用,刀具碰了就记录进去位置了。所以如果是多种类小批量加工最好使用对刀仪,节约时间。
3、自动对刀
自动对刀是通过刀尖检测系统实现的,刀尖以设定的速度向接触式传感器接近,当刀尖与传感器接触并发出信号,数控系统立即记下该瞬间的坐标值,并自动修正刀具补偿值。
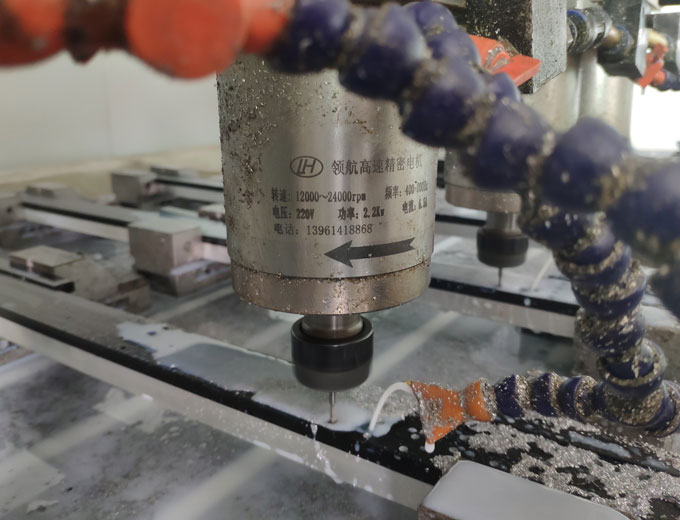
对刀原理:
深入了解雕刻机的对刀原理对于操作者保持清晰地对刀思路、熟练掌握对刀操作以及提出新的对刀方法都具有知道意义。对刀的目的是为了建立工件坐标系,直观的说法是,对刀是确立工件在雕刻机工作台中的位置,实际上就是求对刀点在工作台坐标系中的坐标。对于雕刻机来说,在加工前首先要选择对刀点,对刀点是指用雕刻机加工工件时,刀具相对于工件运动的起点。对刀点既可以设在工件上(如工件上的设计基准或定位基准),也可以设在夹具或工作台上,若设在夹具或工作台上的某一点,则该点必须与工件的定位基准保持一定精度的尺寸关系。
对刀时,应使指刀位点与对刀点重合,所谓刀位点是指刀具的定位基准点,对于雕刻刀来说,其刀位点是刀尖。对刀的目的是确定对刀点(或工件原点)在工作台坐标系中的绝对坐标值,测量刀具的刀位偏差值。对刀点找正的准确度直接影响加工精度。在实际加工工件时,使用一把刀具一般不能满足工件的加工要求,通常要使用多把刀具进行加工。在使用多把雕刻刀加工时,在换刀位置不变的情况下,换刀后刀尖点的几何位置将出现差异,这就要求不同的刀具在不同的起始位置开始加工时,都能保证程序正常运行。为了解决这个问题,雕刻机配备了刀具几何位置补偿的功能,利用刀具几何位置补偿功能,只要事先把每把刀相对于某一预先选定的基准刀的位置偏差测量出来,输入到雕刻机的刀具参数补正栏指定组号里,在加工程序中利用T指令,即可在刀具轨迹中自动补偿刀具位置偏差。刀具位置偏差的测量同样也需通过对刀操作来实现。